Introduction
In today’s fast-paced business landscape, maintaining operational efficiency is paramount. Proactive maintenance has emerged as a pivotal strategy, enabling organizations to mitigate potential issues before they escalate into costly problems. This approach not only enhances the lifespan of equipment but also contributes significantly to productivity and safety in the workplace.
Definition of Proactive Maintenance
Proactive maintenance refers to the strategies and techniques employed to anticipate potential equipment failures before they occur. Instead of waiting for machinery to break down, organizations that implement proactive maintenance schedules regular inspections, maintenance tasks, and data analysis to identify and address wear and tear. This encompasses preventive measures such as routine servicing and predictive analyses, leveraging technology to forecast failures based on historical data and usage patterns.
Importance of Proactive Maintenance in Businesses
Implementing a proactive maintenance strategy is essential for several reasons. Firstly, it significantly reduces downtime, ensuring that operations remain uninterrupted and productive. Secondly, it can lead to substantial cost savings as businesses avoid the high expenses associated with emergency repairs and equipment replacement. Moreover, maintaining equipment in optimal condition enhances safety and compliance, thereby protecting employees from potential hazards linked to faulty machinery. Companies that prioritize proactive maintenance not only foster a culture of care and responsibility but also position themselves competitively in their markets. By investing in this approach, businesses can achieve long-term success and sustainability, ultimately leading to increased profitability and growth.
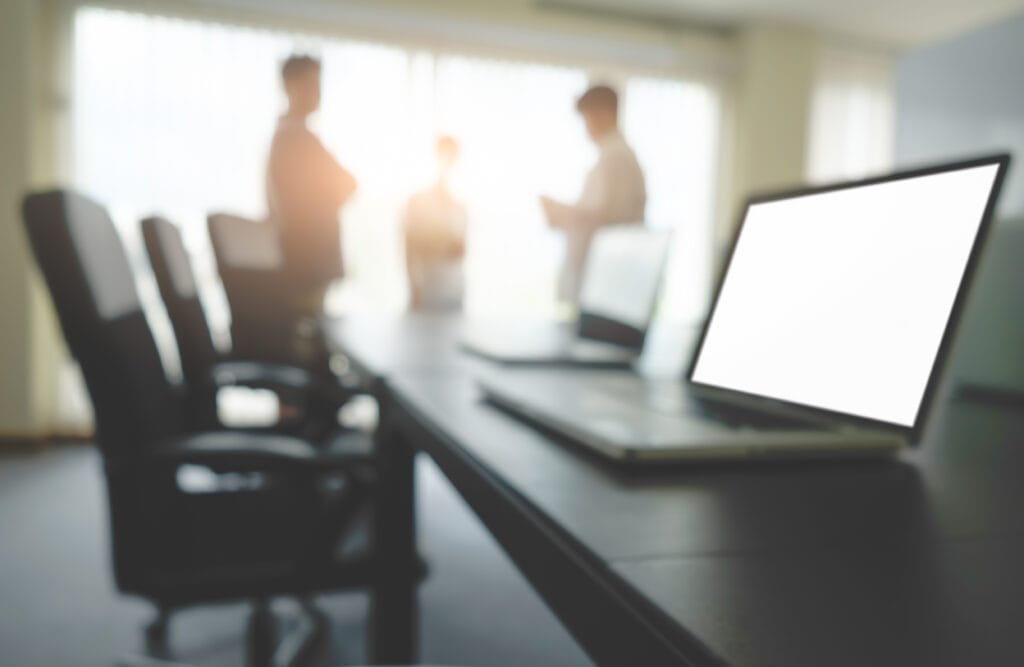
Cost Benefits of Proactive Maintenance
Organizations increasingly recognize the considerable financial advantages of implementing proactive maintenance strategies. By effectively utilizing resources and time, businesses can ensure smooth operations and safeguard their bottom line. Below are some primary cost benefits associated with proactive maintenance.
Reduced Downtime
One of the most significant cost-related benefits of proactive maintenance is the reduction in downtime. Unexpected equipment failures can halt production, leading to lost revenue and inefficient resource utilization. Through regular inspections and preventive measures, organizations can minimize the likelihood of breakdowns, ensuring that operations remain consistent and productive. This stability translates to valuable savings and allows businesses to meet client demands promptly without scrambling to address unforeseen issues.
Extended Equipment Lifespan
Another notable financial benefit is the extended lifespan of equipment. Proactive maintenance practices allow businesses to identify potential problems before they escalate, which means they can address minor issues effectively rather than dealing with major repairs or replacements. Regular servicing not only keeps machinery in optimal working condition but also helps maintain its value over time. As a result, companies can enjoy significant savings by delaying capital expenditures and maximizing their investments in equipment. By fostering a culture of proactive maintenance, organizations can ensure that both their assets and workforce remain productive, further enhancing operational efficiency and overall profitability. Ultimately, the financial benefits derived from proactive maintenance strategies significantly contribute to a sustainable and competitive business model.
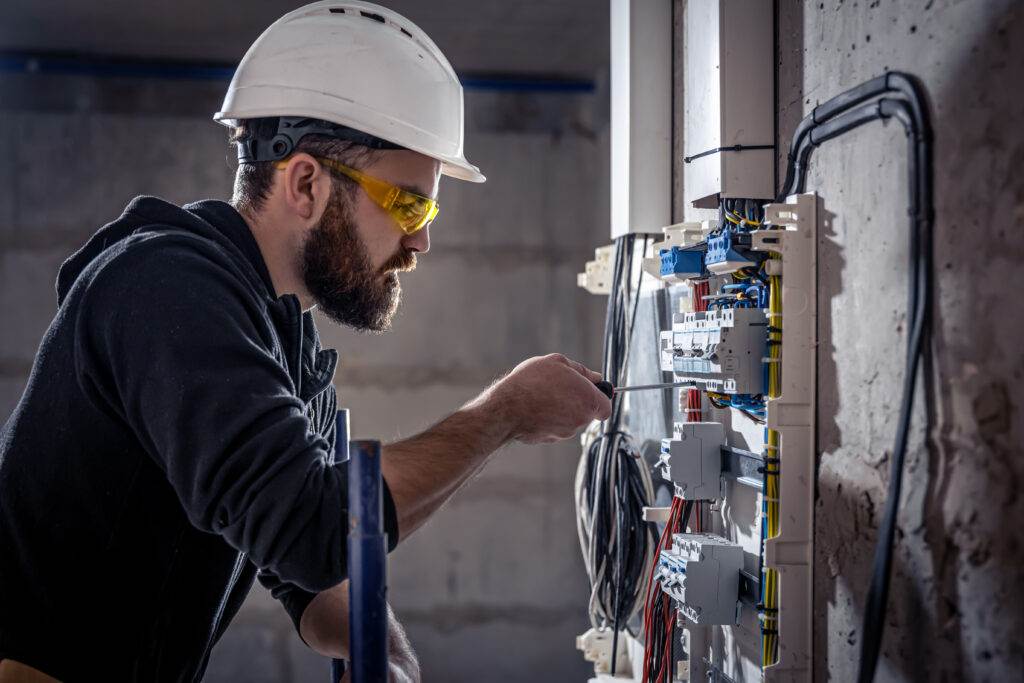
Improved Efficiency through Proactive Maintenance
Proactive maintenance not only results in cost savings but also enhances operational efficiency. By prioritizing maintenance efforts, organizations can achieve smoother workflows and foster a more reliable work environment. Below are key aspects of how proactive maintenance translates into improved efficiency.
Preventing Costly Breakdowns
An essential element of proactive maintenance is its capacity to prevent costly equipment breakdowns. Organizations that actively implement proactive strategies can predict and address potential issues before they disrupt operations. This proactive approach ensures that machinery operates at peak performance levels and significantly reduces the likelihood of unexpected failures that can lead to expensive downtimes. By scheduling routine inspections and maintenance tasks, businesses can maintain optimal operating conditions, thereby protecting their productivity and financial resources.
Optimal Performance
In addition to preventing breakdowns, proactive maintenance fosters optimal performance across all equipment. Regular check-ups and performance assessments enable organizations to identify and rectify inefficiencies or irregularities that may arise. Consequently, this contributes to a working environment characterized by higher productivity rates and consistent output quality. Organizations that invest in proactive maintenance not only enhance the reliability of their equipment but also boost employee morale, as workers can depend on well-maintained machinery for their daily tasks. As a result, enhanced efficiency through proactive maintenance leads to improved organizational resilience, reduces operational bottlenecks, and drives overall business growth. Ultimately, adopting a proactive maintenance strategy equips organizations to operate more efficiently while positioning them advantageously in the competitive marketplace.
Safety Advantages of Proactive Maintenance
Proactive maintenance not only enhances efficiency but also contributes significantly to workplace safety. Organizations that prioritize a proactive maintenance strategy can create a safer working environment for their employees. Below are key insights into how proactive maintenance translates into safety advantages.
Ensuring Workplace Safety
One of the primary benefits of proactive maintenance is its capacity to ensure workplace safety. By routinely inspecting and maintaining equipment, organizations can identify and eliminate potential hazards before incidents occur. This proactive approach enables businesses to rectify faults or deficiencies in machinery, substantially decreasing the risk of accidents. Employees are less likely to encounter safety issues when working with well-maintained tools and equipment. In essence, organizations demonstrate a commitment to employee wellbeing by fostering a culture of safety through regular maintenance checks and procedural diligence.
Compliance with Regulations
Moreover, proactive maintenance plays a crucial role in ensuring compliance with industry regulations and safety standards. Various sectors impose stringent requirements for equipment upkeep and workplace safety. By proactively maintaining their operations, organizations can avoid costly fines and legal repercussions that arise from non-compliance. Consistent maintenance not only adheres to regulatory frameworks but also instills a culture of responsibility and accountability within the workforce. Employees recognize their employer’s dedication to maintaining safety and compliance standards, cultivating a sense of trust and morale. Through these efforts, businesses can operate with confidence, safeguarding both their operations and their most valuable asset – their employees. Thus, investing in proactive maintenance is not just a strategic decision for efficiency but also a vital aspect of ensuring safety in the workplace.
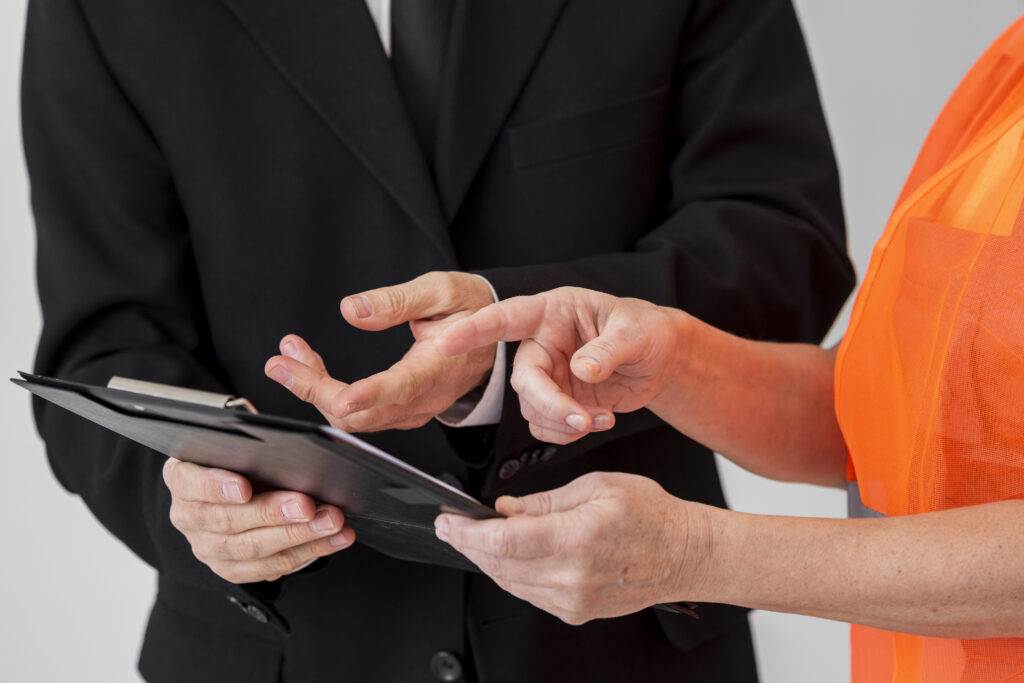
Decreased Repair and Replacement Costs
Proactive maintenance not only enhances safety and operational efficiency but also results in significant cost savings for organizations. By investing in a proactive maintenance strategy, businesses can minimize repair and replacement costs associated with equipment and facility management. Below are key aspects of how proactive maintenance can lead to financial benefits.
Early Detection of Issues
One of the most valuable features of proactive maintenance is the early detection of issues before they escalate into major problems. Regular inspections and monitoring allow organizations to identify wear and tear, abnormal operating conditions, or potential failures. This early intervention means that minor repairs can be conducted, preventing larger, more costly repairs down the line. As a result, organizations can save both time and financial resources, optimizing their maintenance budgets.
Avoiding Major Repairs
Moreover, when businesses implement proactive maintenance, the likelihood of facing unexpected breakdowns is dramatically reduced. Equipment that is maintained regularly is less prone to catastrophic failures, which often necessitate expensive repairs or complete replacements. By avoiding these major repairs, organizations can allocate their budgets more effectively, thus promoting better financial health. Additionally, a well-maintained and reliable fleet of machinery fosters a smooth operational flow, further supporting cost efficiency. In essence, embracing proactive maintenance not only fortifies safety and compliance but also serves as a compelling financial strategy, necessitating a careful evaluation of maintenance investments to reap long-term savings.