Introduction
In today’s industrial world, managing hazardous materials in the workplace is of utmost importance. Companies that prioritize safety and compliance not only safeguard their employees but also enhance their operational efficiency and credibility in their industry.
Importance of Managing Hazardous Materials in the Workplace
Every organization that deals with hazardous materials must recognize that proper management is critical for preventing accidents and ensuring employee welfare. Hazardous materials can pose various risks, including health hazards, environmental contamination, and serious workplace incidents. By implementing comprehensive management strategies, companies can reduce the likelihood of exposure and accidents. This not only fosters a safer work environment but also contributes to employee morale and productivity. Furthermore, good practices in hazardous material management can improve a company’s reputation, demonstrating a commitment to safety that is attractive to clients and stakeholders.
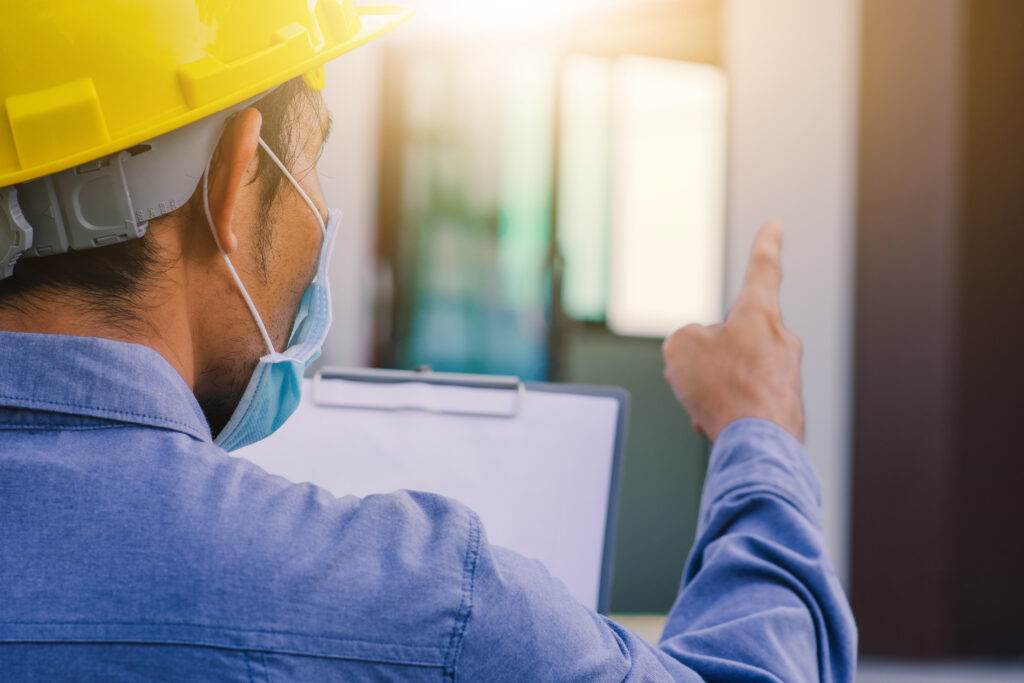
Legal Regulations and Compliance
Complying with legal regulations concerning hazardous materials is not just a matter of ethics; it’s a legal obligation. Various government agencies oversee the handling, storage, and disposal of hazardous materials, imposing penalties for non-compliance. Organizations must stay informed about local, state, and federal regulations to avoid costly fines and legal challenges. By adhering to these regulations, companies protect not only their employees but also their assets and the environment. A robust legal compliance strategy includes regular training programs for employees, thorough risk assessments, and the establishment of an effective management system for hazardous substances. Such measures ensure a workplace that is not only legally compliant but also defines industry standards for safety and responsibility.
Identifying Hazardous Materials
Classification of Hazardous Materials
Identifying hazardous materials requires a thorough understanding of their classifications, which can greatly aid in proper management. Hazardous materials are generally divided into several categories based on their properties and potential risks. These categories include flammable substances, corrosive materials, reactive substances, and toxic agents. Each classification presents unique challenges that organizations must address when developing management strategies. Recognizing these classifications enables companies to implement targeted safety measures and training protocols to mitigate potential hazards effectively.
Common Hazardous Materials Found in Workplaces
Various industries deal with hazardous materials regularly, and understanding what these materials are is crucial for maintaining safety. Common hazardous materials found in workplaces include chemicals such as solvents, acids, and heavy metals. Additionally, biological hazards, such as pathogens, may be present in healthcare settings. Other examples include asbestos found in older buildings and flammable liquids used in manufacturing processes. Organizations must inventory these hazardous substances, assess their risks, and establish proper handling, storage, and disposal procedures. Regular training on the safe use of these materials can further ensure that all employees are aware of the potential dangers and equipped to handle them safely. In summary, a meticulous identification process is essential for maintaining a safe work environment and complying with legal requirements, ultimately protecting employees and enhancing overall organizational safety.
Risk Assessment and Management
Conducting Hazard Assessments
Conducting hazard assessments is a critical step in identifying and mitigating risks associated with hazardous materials in the workplace. Organizations should regularly evaluate their operations to determine potential hazards related to the substances being used. This involves thorough inspections to identify the presence of hazardous materials, assessing their physical and chemical properties, and understanding how they interact with the work environment. Regular assessments not only help in identifying existing hazards but also in predicting potential risks that could arise from changes in processes or the introduction of new materials. By documenting findings and maintaining an up-to-date inventory of hazardous materials, companies can stay ahead of possible dangers and enhance safety.
Implementing Control Measures
Once hazardous materials have been identified and assessed, the next step is to implement effective control measures to minimize risks. Organizations should develop a comprehensive safety plan that includes procedures for safe handling, storage, and disposal of hazardous substances. This plan should also encompass ventilation systems, personal protective equipment (PPE), and staff training programs aimed at educating employees on the correct practices for managing hazardous materials. Regular reviews and updates to safety protocols are vital, ensuring that they continue to meet regulatory requirements and adapt to changes within the organization. By prioritizing risk assessment and the integration of robust control measures, businesses can create a safer working environment, reducing the likelihood of accidents and ensuring compliance with occupational safety standards.
Handling and Storage Procedures
Safe Handling Practices
Safe handling practices are essential for reducing the risk of accidents and ensuring the health and safety of employees when dealing with hazardous materials. Organizations must provide training for all employees on the risks associated with specific substances and the correct procedures for handling them safely. This training should cover fundamental aspects such as the use of appropriate personal protective equipment (PPE), understanding Material Safety Data Sheets (MSDS), and recognizing emergency protocols. By fostering a culture of safety awareness, organizations can empower their employees to adopt best practices consistently while minimizing exposure to hazards. Additionally, implementing clear procedures for reporting safety incidents or potential hazards can enhance overall workplace safety.
Proper Storage Techniques
Proper storage techniques are critical in managing hazardous materials effectively. Organizations should ensure that hazardous substances are stored in designated areas that comply with regulatory requirements and are clearly labeled. This includes using approved containers that are compatible with the materials stored within them and maintaining adequate segregation of incompatible substances to prevent chemical reactions. Furthermore, proper ventilation must be ensured in storage areas to minimize the build-up of harmful fumes. Regular inspections of storage facilities can help identify potential hazards such as leaks or deterioration of containers, allowing for timely corrective actions. By adhering to rigorous storage standards, businesses can significantly mitigate the risks associated with hazardous materials and bolster overall workplace safety.
Personal Protective Equipment (PPE)
Importance of PPE in Hazardous Material Management
Personal Protective Equipment (PPE) plays a vital role in safeguarding employees from a range of hazards associated with handling and storing hazardous materials. Employers must ensure that all personnel are equipped with the appropriate PPE to minimize exposure to dangerous substances. Training employees on the correct use and maintenance of PPE is essential for maximizing its effectiveness. Furthermore, a strong organizational commitment to enforcing PPE protocols can foster a culture of safety, reducing the likelihood of accidents and promoting a healthier work environment. By recognizing the significance of PPE, organizations can better protect their workforce while also demonstrating their dedication to employee well-being.
Types of PPE for Different Hazardous Materials
Selecting the appropriate type of PPE is crucial based on the nature of the hazardous materials being handled. Common types of PPE include gloves, safety goggles, face shields, respiratory protection, and specialized suits. For example, when dealing with chemicals that can cause skin irritation, impervious gloves and full-body suits may be necessary. In environments where harmful dust or fumes are present, respiratory protection becomes essential. Organizations should conduct thorough risk assessments to identify the specific hazards their employees may face and choose PPE accordingly. Regular training sessions should also be implemented to keep staff informed about the latest PPE standards and advances. By prioritizing the right PPE, organizations can significantly enhance workplace safety and effectively manage hazardous material risks.
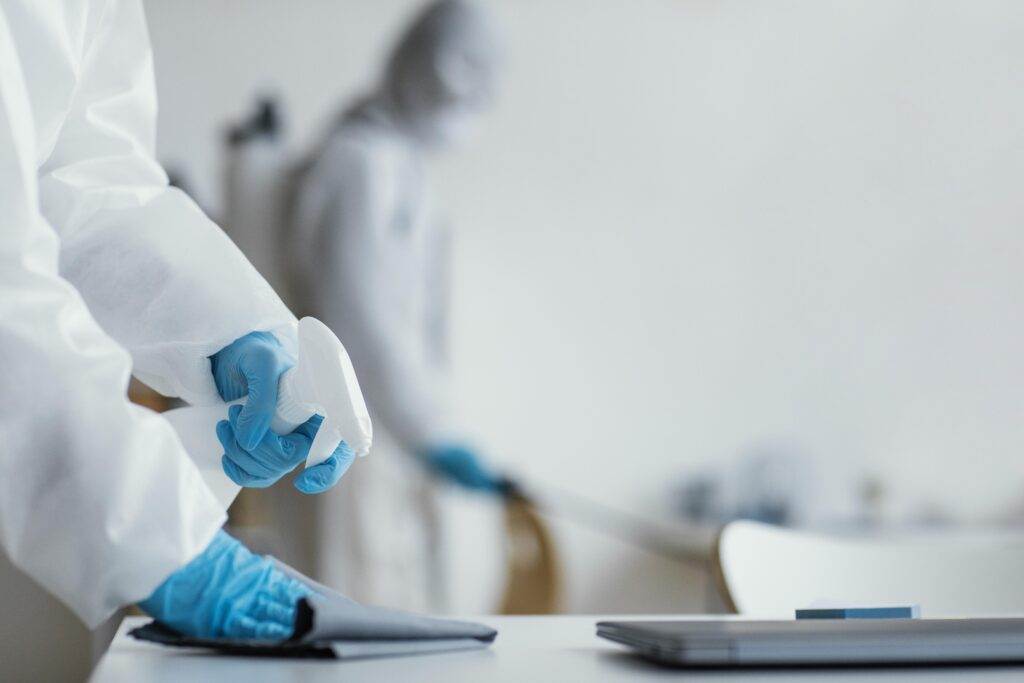
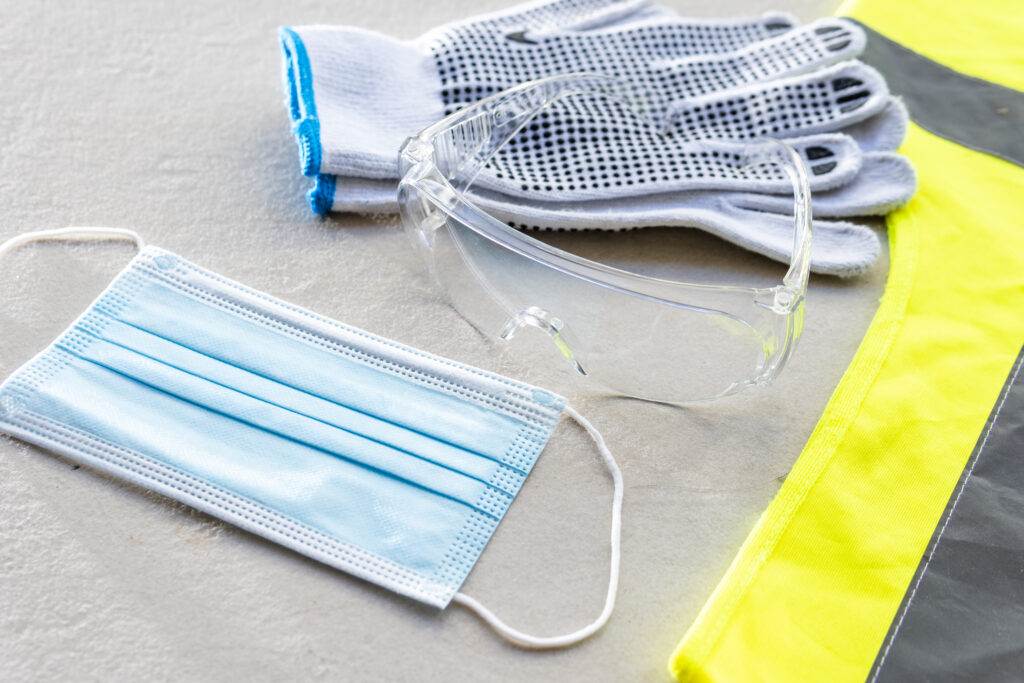
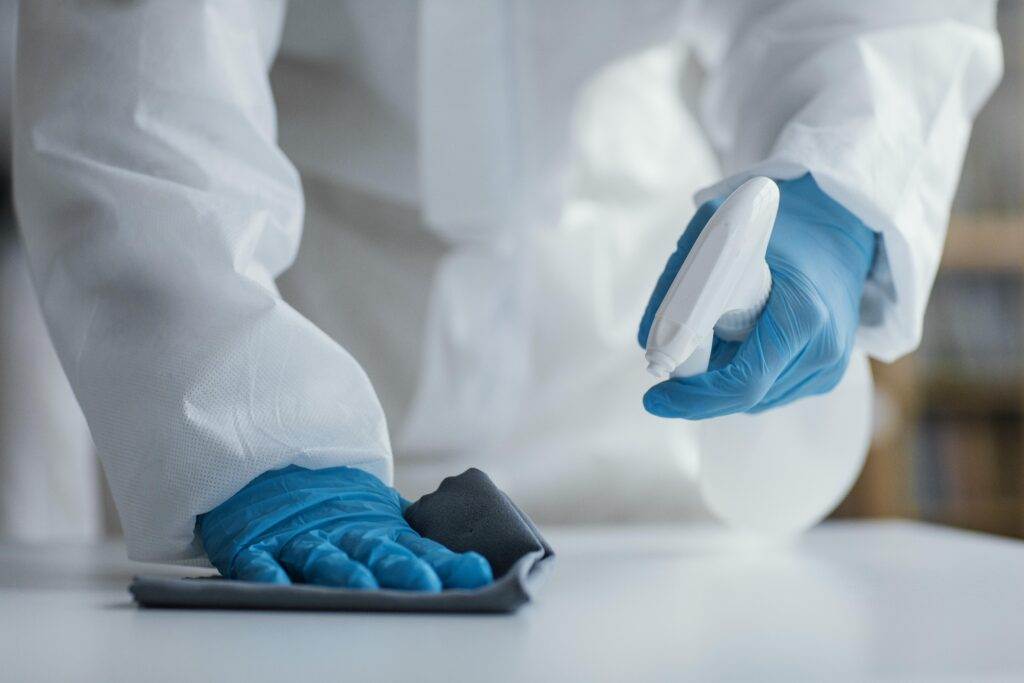