Understanding OSHA Compliance
Overview of OSHA Regulations
The Occupational Safety and Health Administration (OSHA) was established to ensure safe and healthful working conditions for employees across various industries. OSHA regulations encompass a wide range of standards that address numerous workplace hazards, from chemical exposure to machinery safety. Each regulation is designed to protect employees from potential dangers, requiring employers to implement safety protocols and maintain a hazard-free environment. Some key areas of OSHA regulations include:
- General Duty Clause: Employers are required to provide a workplace that is free from recognized hazards.
- Recordkeeping: Employers must maintain accurate records of employee injuries and illnesses.
- Training Requirements: Specific training must be provided for employees who are exposed to certain hazards.
Importance of OSHA Compliance in the Workplace
Compliance with OSHA standards is not simply a legal requirement; it is crucial for fostering a culture of safety within the organization. When employers prioritize OSHA compliance, they do more than mitigate legal risks—they also enhance employee morale and productivity. The benefits of OSHA compliance are evident:
- Reduced Workplace Injuries: A safer work environment leads to fewer accidents and injuries.
- Lower Insurance Costs: Fewer claims can translate to lower workers’ compensation insurance premiums.
- Enhanced Reputation: Companies that adhere to safety regulations often gain trust and confidence from customers and partners.
Common Violations and Penalties
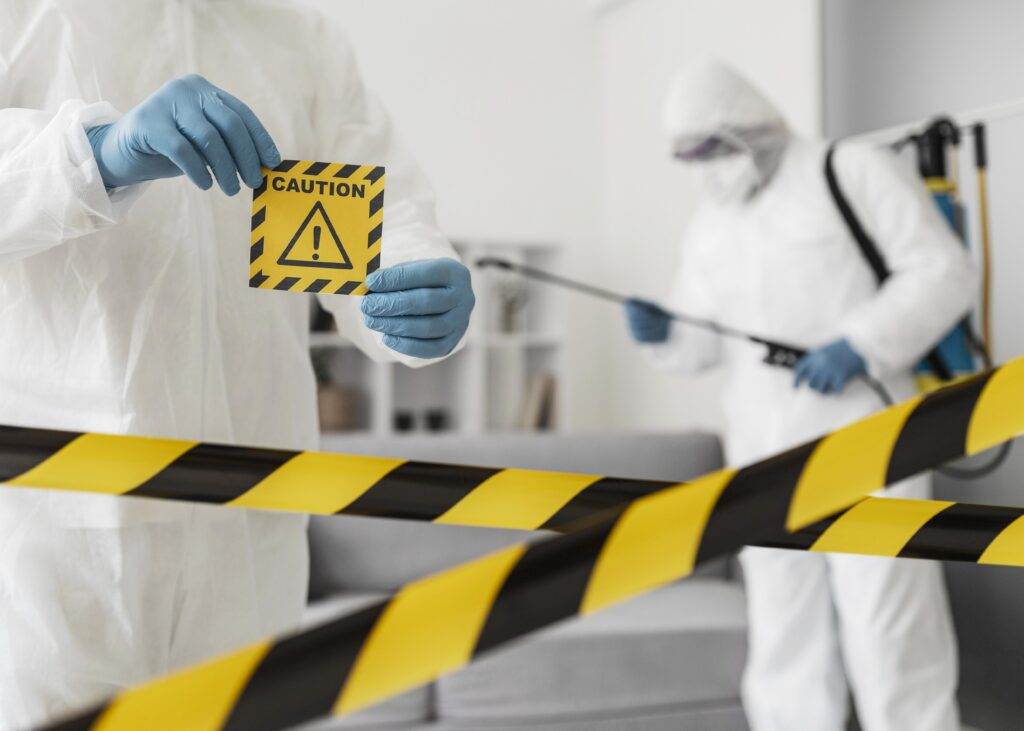
Despite the importance of OSHA compliance, many organizations still face numerous violations. Some of the most common infractions include:
- Failure to Provide Proper PPE: Many employers underestimate the importance of Personal Protective Equipment, resulting in fines.
- Inadequate Training: Employees must be properly trained on safety procedures; failure to do so can lead to severe penalties.
- Poor Recordkeeping: Inaccurate documentation can result in significant fines and scrutiny.
Penalties for violating OSHA regulations can be serious, ranging from minor fines for non-compliance to substantial penalties for egregious violations. The impact of these violations not only affects financial standings but can also lead to harmful consequences for employees. Understanding OSHA compliance is essential for any workplace looking to foster safety, protect employees, and avoid the repercussions of negligence.
Establishing an OSHA Compliance Program
To foster a safe and compliant workplace, establishing an OSHA compliance program is essential. A comprehensive program not only helps in addressing workplace hazards but also promotes a culture of safety among employees. Implementing the key components of this program can significantly reduce the likelihood of accidents and injuries.
Appointing a Safety Officer
One of the first steps in establishing an OSHA compliance program is appointing a dedicated safety officer. This individual plays a crucial role in overseeing safety procedures and ensuring compliance with OSHA regulations. Key responsibilities of a safety officer include:
- Monitoring Compliance: Keeping track of aspects of local, state, and federal regulations.
- Inspecting the Workplace: Regularly assessing the environment for potential hazards.
- Acting as a Liaison: Communicating safety information between management and employees.
By having a dedicated resource focused on safety, organizations can improve their response to safety issues and promote proactive measures.
Conducting Regular Safety Inspections
Regular safety inspections are vital for identifying hazards before they lead to accidents. Routine assessments allow for ongoing evaluations of workplace safety and adherence to OSHA standards.
- Types of Inspections:
- Scheduled Inspections: Regularly conducted at designated times, such as monthly or quarterly.
- Surprise Inspections: Unannounced checks that can reveal real-time situations and challenges.
Organizations should utilize inspection checklists that cover common hazards specific to their industry. Such documentation not only aids in compliance but also builds a foundation for continuous improvement.
Providing Employee Training on Safety Procedures
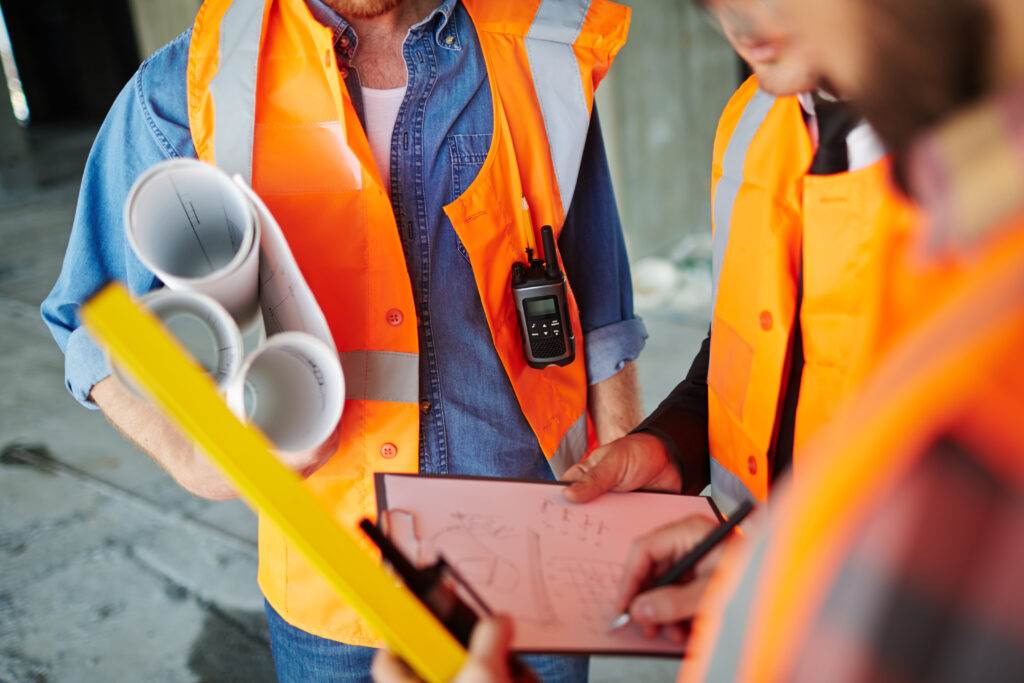
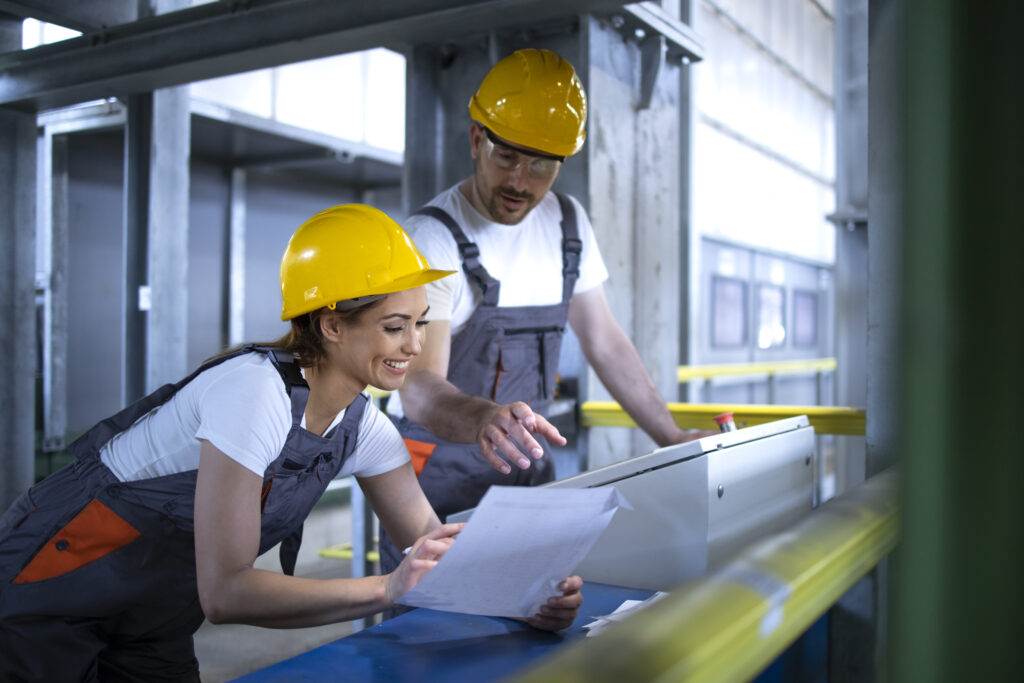
Training is arguably the most critical component of an OSHA compliance program. Employees need to understand safety procedures to effectively reduce risks in the workplace.
- Essential Training Topics:
- Proper Use of PPE: Ensuring employees know how to correctly use and maintain personal protective equipment.
- Emergency Response Protocols: Training employees on what to do in case of a fire, chemical spill, or accident.
- Hazard Recognition: Educating employees on how to identify hazards in their work environment.
Regular training sessions not only fulfill legal obligations but also empower employees to prioritize their safety and the safety of their colleagues. By taking these proactive steps, organizations can create a robust OSHA compliance program that effectively protects employees while maintaining adherence to regulations.
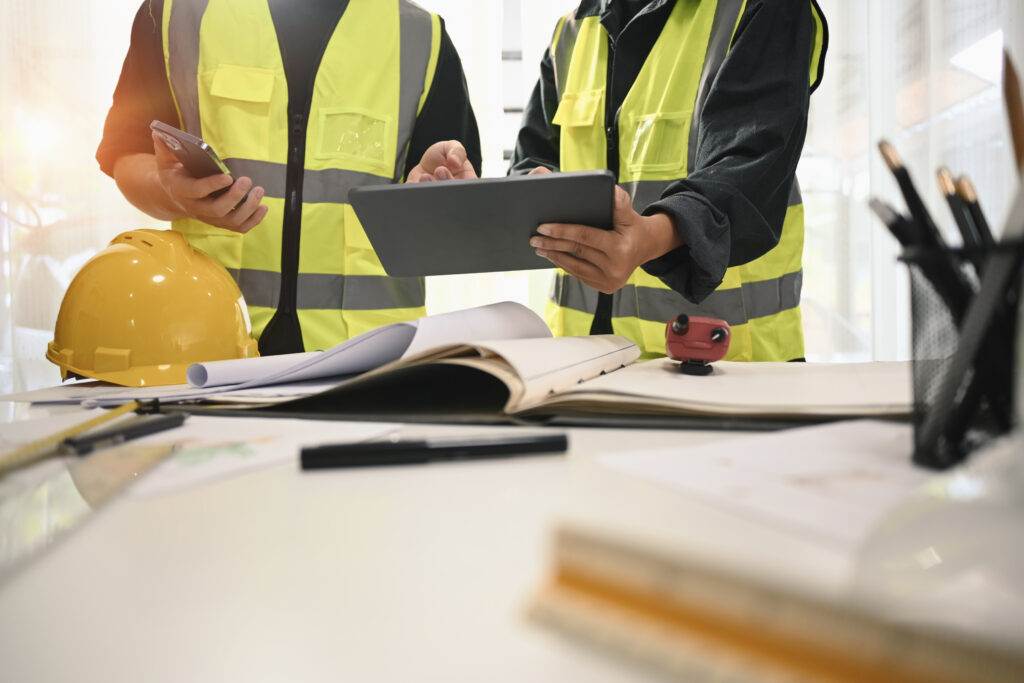
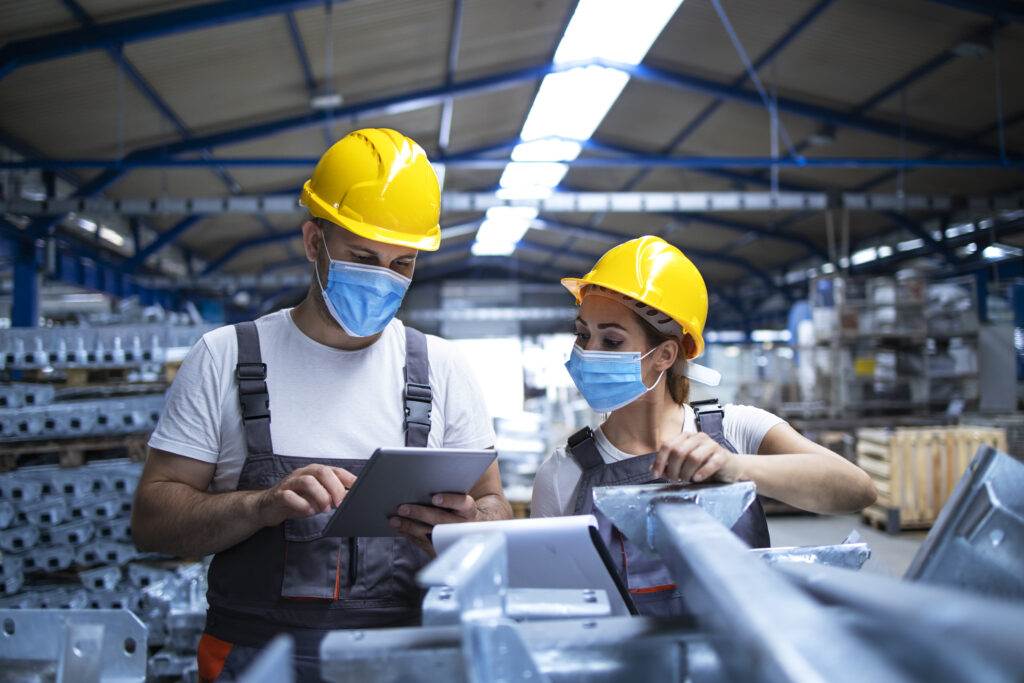
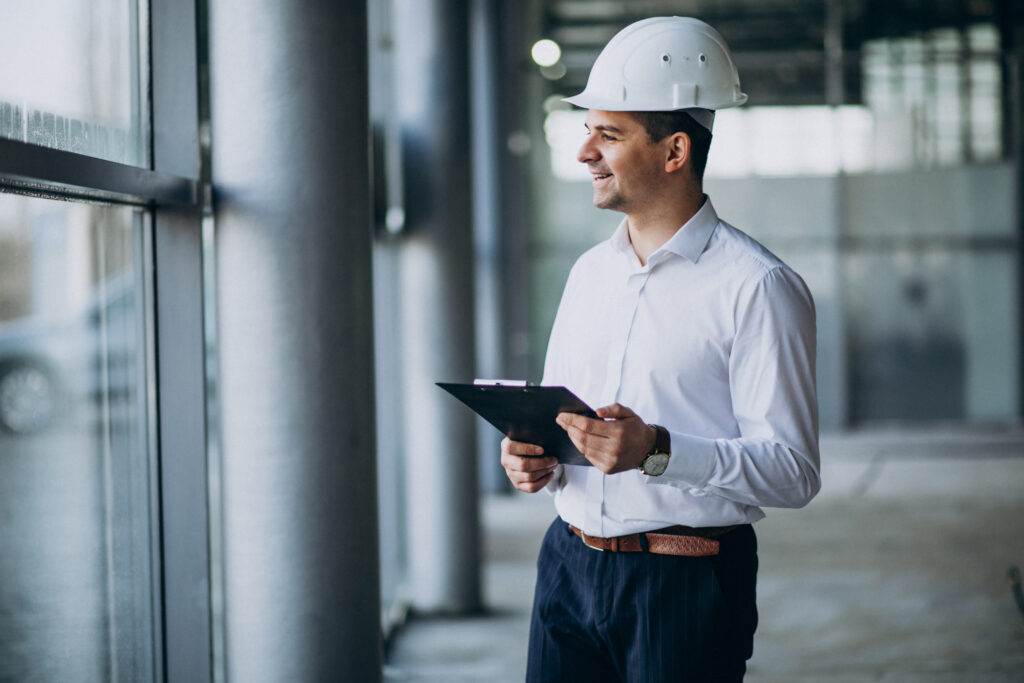
Ensuring Safety Protocols and Procedures
With a solid OSHA compliance program in place, the next step is to ensure that safety protocols and procedures are actively maintained and followed throughout the workplace. Comprehensive safety measures not only protect employees but also cultivate a culture of care and responsibility. Three critical areas to focus on include Personal Protective Equipment (PPE) requirements, emergency action plans, and hazard communication standards.
Personal Protective Equipment (PPE) Requirements
Personal Protective Equipment (PPE) forms the first line of defense against workplace hazards. Employers are required to assess the risks associated with their specific work environment and provide the necessary protective gear to their employees. Some standard PPE includes:
- Safety Helmets: Protect against head injuries from falling objects.
- Eye Protection: Safety goggles or face shields to prevent eye injuries.
- Hearing Protection: Earplugs or earmuffs to shield against noise-induced hearing loss.
Regular training sessions should be held to educate employees on the proper use, maintenance, and limitations of PPE. Clear signage reminding employees to wear their PPE can also help reinforce its importance.
Emergency Action Plans and Response
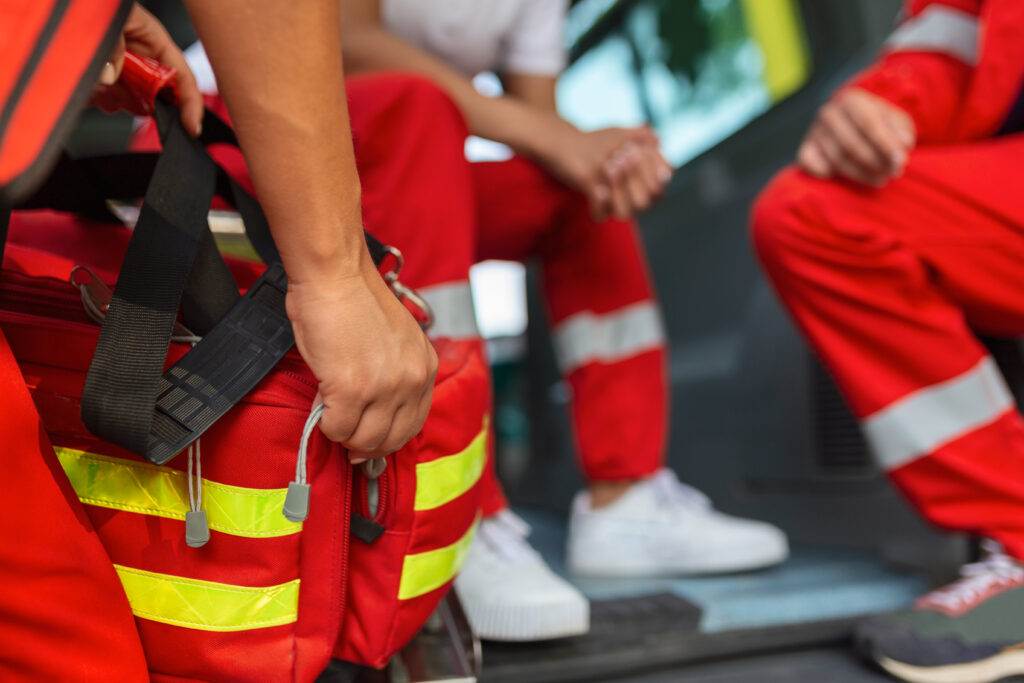
In any workplace, the unexpected can happen at any moment, making it crucial to have a well-defined emergency action plan. This plan outlines the procedures for responding to various emergencies, such as fires, medical incidents, or natural disasters. Key components of an emergency action plan include:
- Evacuation Procedures: Clearly outlined routes and designated assembly points.
- Emergency Contacts: A list of key personnel and emergency services.
- Drills and Training: Regular drills to familiarize employees with emergency procedures.
By conducting mock drills and providing constant updates on the action plan, employers can prepare employees to respond effectively in a crisis.
Hazard Communication Standards
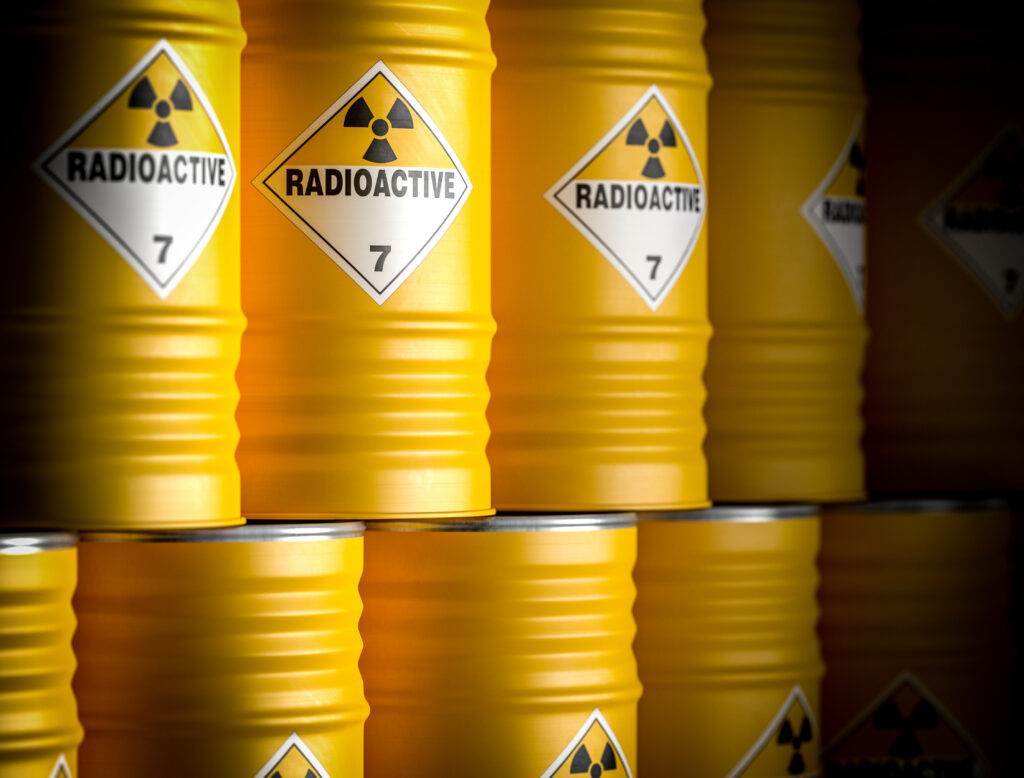
Effective communication regarding workplace hazards is paramount for keeping employees safe. OSHA has implemented Hazard Communication Standards (HCS) that mandate employers to inform workers of hazardous chemicals they may encounter. To comply with HCS, employers must:
- Label Containers: Ensure that all chemical containers are appropriately labeled with hazard information.
- Safety Data Sheets (SDS): Maintain accessible sheets that provide detailed information about handling and emergency response for each chemical.
- Training Sessions: Provide training on understanding labels and SDS, focusing on the importance of safety measures.
By prioritizing clear communication about hazards, organizations can empower employees to work safely and confidently. In conclusion, maintaining effective safety protocols and procedures is essential for ensuring a safe and compliant work environment. Through the diligent implementation of PPE requirements, emergency action plans, and hazard communication standards, organizations can significantly enhance workplace safety.
Maintaining OSHA Recordkeeping and Reporting
Once robust safety protocols and procedures are in place, maintaining proper recordkeeping and reporting becomes the backbone of an effective OSHA compliance program. Accurate documentation helps organizations track incidents and ensure compliance with regulations, ultimately creating a safer workplace. This section focuses on three critical elements: injury and illness recordkeeping, OSHA reporting requirements, and the retention of records.
Injury and Illness Recordkeeping
Documenting workplace injuries and illnesses not only serves as a legal requirement, it also provides valuable data for improving safety measures. Employers are mandated to maintain an OSHA 300 Log, which records the specifics of any work-related injuries or illnesses. Key aspects of injury and illness recordkeeping include:
- Timeliness: Record incidents within seven days to ensure accuracy and compliance.
- Detailing: Include all necessary information such as the date of the incident, the nature of the injury, and treatment provided.
- Privacy: Safeguard the personal information of affected employees while ensuring necessary details are made available for analysis.
This systematic approach allows organizations to identify trends and address prevalent hazards effectively.
OSHA Reporting Requirements
In addition to maintaining records, employers must adhere to specific reporting requirements. Certain severe incidents must be reported directly to OSHA within a defined timeframe. Employers need to report:
- Work-related fatalities: Must be reported within eight hours.
- Severe injuries: Such as amputations, loss of an eye, or hospitalization, must be reported within 24 hours.
Understanding these requirements helps organizations avoid penalties and demonstrate their commitment to workplace safety.
Retention of Records
Moreover, retention of safety records is crucial for both compliance and reference. Organizations must keep OSHA records for a specific duration:
- OSHA 300 Log: Retain for five years following the end of the year it covers.
- Incident Reports and OSHA forms (e.g., 300A): Keep for at least five years as well.
Regular audits of recordkeeping practices can ensure that records are being maintained properly, which reinforces an organization’s proactive stance on safety. In conclusion, maintaining comprehensive OSHA recordkeeping and reporting practices is vital for identifying risks and fostering a safer workplace. By diligently managing injury and illness logs, adhering to reporting requirements, and retaining records, organizations can not only comply with regulations but also enhance their overall safety culture.
Responding to OSHA Inspections and Citations
Maintaining OSHA compliance is a continuous journey, and part of that journey includes being prepared for potential inspections and citations. Understanding how to handle these situations effectively can significantly impact an organization’s safety culture and overall compliance. This section will delve into handling OSHA inspections, understanding the citation process, and ways to correct violations while preventing future occurrences.
Handling OSHA Inspections Effectively
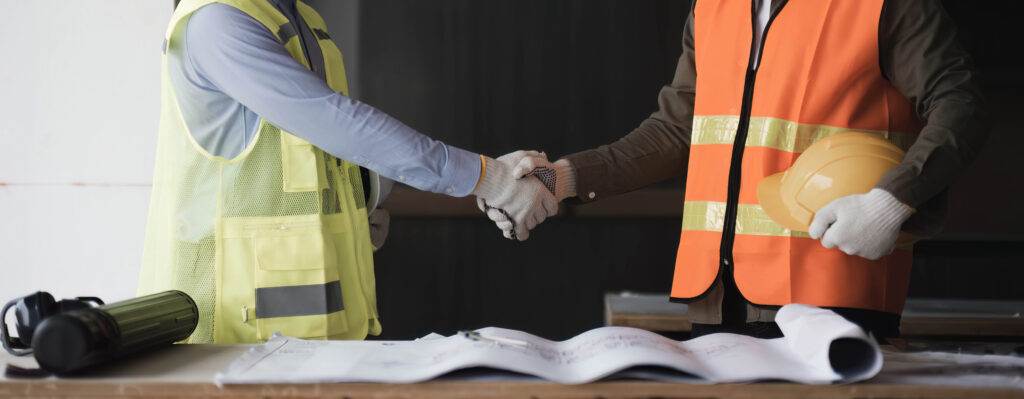
When an OSHA inspector arrives at your workplace, it’s essential to handle the situation with professionalism and composure. Preparation is key to managing inspections effectively. Here are some best practices:
- Designate a Point of Contact: Have a trained individual—like the safety officer—assigned to communicate with the inspector.
- Stay Calm and Cooperative: Answer questions honestly and provide requested documentation while maintaining a professional demeanor.
- Conduct a Pre-Inspection Walkthrough: Identify potential hazards before inspections, which not only aids in preparation but also reflects a proactive attitude towards safety.
Being well-prepared can create a positive impression and demonstrate the organization’s commitment to safety.
Understanding the Citation Process
If violations are found during an inspection, OSHA will issue citations. Understanding the citation process can help organizations respond appropriately. Citations are usually categorized based on severity, including:
- Serious: There is a substantial probability of death or serious injury.
- Willful: The employer knowingly failed to comply with a legal requirement.
- Other-than-serious: Typically relate to safety and health concerns but don’t pose an immediate threat.
Organizations have the right to contest citations within a certain timeframe, and knowing how to navigate this process can help mitigate penalties and improve safety standards.
Correcting Violations and Preventing Recurrence
Upon receiving a citation, the focus should shift to correcting the identified violations promptly and implementing measures to prevent recurrence. Key steps include:
- Developing an Action Plan: Outline how to address each violation, including timelines and responsible parties.
- Training and Education: Reinforce safety training to ensure all employees understand revised procedures and compliance requirements.
- Follow-Up Inspections: Conduct internal inspections to ensure corrective actions have been effectively implemented.
By proactively addressing violations and fostering an environment of continuous improvement, organizations can minimize future risks and further enhance workplace safety. In conclusion, responding to OSHA inspections and citations requires a strategic approach that encompasses effective handling of inspectors, understanding the citation process, and continuously working to correct issues. By adopting these practices, organizations can not only comply with regulations but also cultivate a more robust safety culture.