Introduction
Importance of Maintenance Schedules
Effective maintenance schedules play a critical role in ensuring the longevity and performance of equipment and systems across various sectors. Proper scheduling not only minimizes the risk of unexpected equipment failures but also optimizes resource allocation. When maintenance is performed regularly and systematically, organizations can:
- Avoid costly repairs: Unexpected breakdowns are often accompanied by high repair costs and lost productivity.
- Enhance safety: Regular maintenance reduces the risk of accidents caused by malfunctioning machinery.
- Boost productivity: Well-maintained equipment operates more efficiently, translating to higher output.
Overview of Operational Efficiency
Operational efficiency is intricately linked to how effectively resources are utilized, including time, labor, and materials. A streamlined maintenance schedule can significantly enhance operational efficiency by ensuring that equipment is always in peak condition. This leads to:
- Reduced Downtime: By anticipating maintenance needs, organizations can plan for downtime, reducing its impact on operations.
- Increased ROI: Properly maintained equipment tends to deliver higher returns, both in terms of performance and investment.
In conclusion, creating and adhering to a thoughtfully developed maintenance schedule is essential for optimizing both equipment performance and overall operational efficiency.
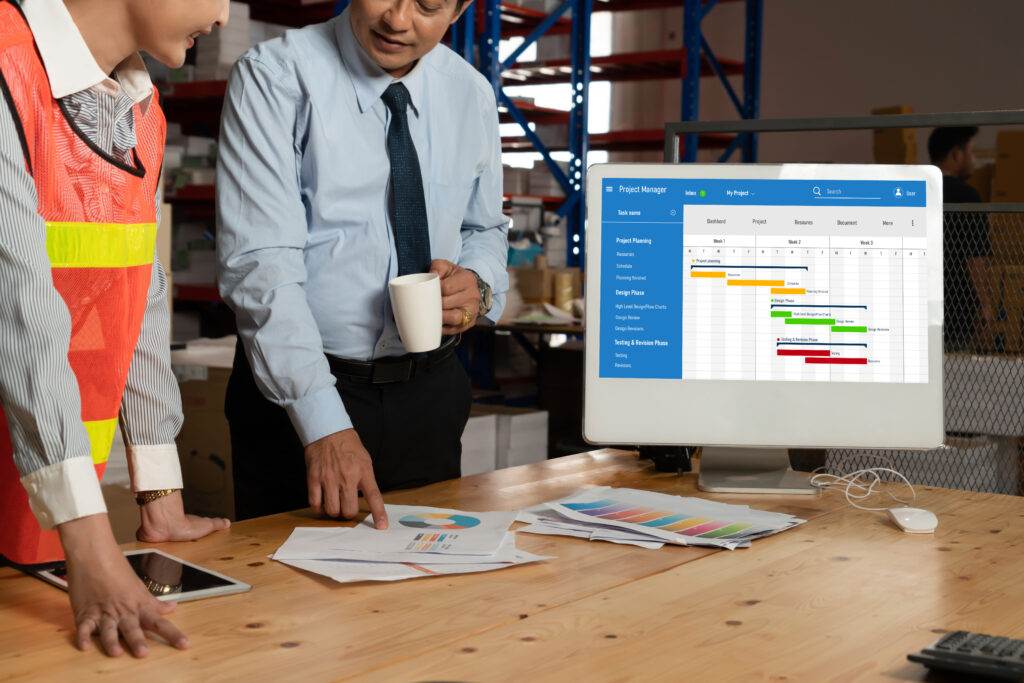
Understanding Maintenance Scheduling
Definition of Maintenance Schedules
Maintenance schedules are structured plans that outline when and how maintenance tasks should be performed on equipment and machinery. These schedules ensure that maintenance activities are conducted consistently, preventing unexpected failures and optimizing performance. Key components of effective maintenance schedules include:
- Frequency: How often maintenance tasks are performed (daily, weekly, monthly).
- Scope: Specific tasks to be completed during each maintenance session.
- Documentation: Recording maintenance activities and findings for future reference.
Types of Maintenance Strategies
Understanding the various maintenance strategies is crucial for developing an effective schedule. Here are the main types:
- Preventive Maintenance: Regularly scheduled maintenance activities aimed at preventing equipment failures before they occur.
- Corrective Maintenance: Performed after a failure has occurred, focusing on fixing the problem.
- Predictive Maintenance: Utilizes data and analytics to predict when maintenance should be performed based on the condition of the equipment rather than on a fixed schedule.
- Reliability-Centered Maintenance (RCM): A strategy that prioritizes maintenance tasks based on the reliability and criticality of the equipment.
By understanding these types, businesses can tailor their maintenance schedules to best fit operational needs, ensuring both efficiency and effectiveness in their maintenance efforts.
Benefits of Tailored Maintenance Schedules
Cost Efficiency
Tailored maintenance schedules significantly enhance cost efficiency for organizations. By proactively addressing maintenance needs, companies can avoid the high expenses associated with emergency repairs and unplanned downtime. Key benefits include:
- Reduced Repair Costs: Regular maintenance prevents larger, more expensive issues from arising.
- Optimized Resource Allocation: Schedules allow for better planning of labor and materials, reducing waste.
Minimizing Downtime
Minimizing downtime is essential in maintaining operational efficiency. A tailored maintenance schedule enables organizations to:
- Schedule Maintenance During Off-Peak Hours: This ensures that essential operations are not disrupted, allowing for continuous productivity.
- Anticipate Needs: By predicting when maintenance should be performed, businesses can effectively reduce unexpected breakdowns.
Extending Equipment Lifespan
Another compelling advantage of customized maintenance is its impact on the lifespan of equipment. Regular care ensures that:
- Machinery Operates Smoothly: Reduced wear and tear prolongs equipment life.
- Investment Protection: Extending the lifespan of assets leads to better returns on investment, as companies can use equipment longer before needing replacements.
In conclusion, tailored maintenance schedules not only foster cost efficiency but also minimize downtime and extend the lifespan of crucial equipment, creating a sustainable operational environment.
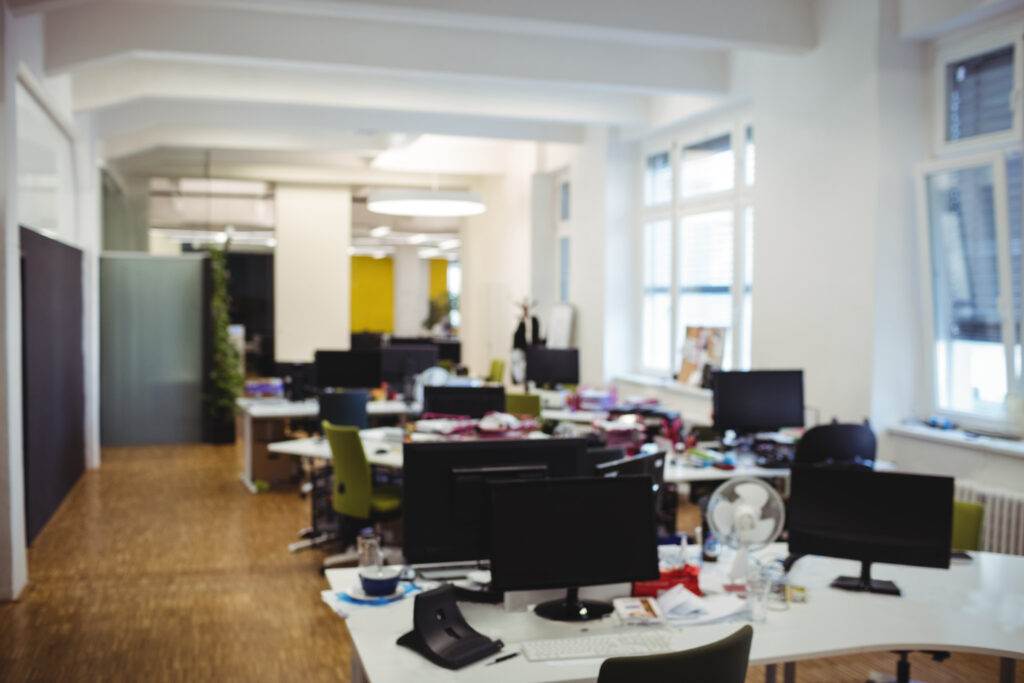
Factors Influencing Maintenance Schedule Optimization
Equipment Type and Usage
One of the most significant factors affecting maintenance schedule optimization is the type and usage of equipment. Different machinery has unique requirements based on:
- Complexity: More complex systems often necessitate more frequent maintenance.
- Usage Patterns: Equipment that is operated intensely will require more rigorous and frequent servicing to avoid wear and tear.
Maintaining a clear understanding of how often and intensively equipment is used allows companies to tailor their maintenance schedules effectively.
Environmental Conditions
Environmental conditions can greatly influence maintenance needs. For instance:
- Temperature and Humidity: Extremes in weather can accelerate wear on equipment, necessitating more frequent checks.
- Cleanliness: Dusty or corrosive environments can affect machine performance, requiring specialized maintenance protocols.
Customizing maintenance schedules to account for these factors helps in preserving equipment integrity over time.
Regulatory Compliance
Finally, regulatory compliance plays a crucial role in determining maintenance schedules. Many industries have specific regulations that dictate:
- Frequency of Inspections: Certain equipment must be inspected at designated intervals to comply with safety standards.
- Documentation Requirements: Proper records of maintenance activities are often legally required.
By incorporating compliance-related aspects into maintenance scheduling, organizations can avoid potential fines and ensure operational safety. Understanding these factors helps align maintenance strategies with organizational goals, promoting overall productivity and efficiency.
Tailoring Maintenance Schedules
Data-Driven Approaches
When it comes to tailoring maintenance schedules, adopting data-driven approaches can significantly enhance effectiveness. By leveraging data analytics, organizations can identify patterns and trends in equipment performance that inform maintenance decisions. Consider the following benefits:
- Real-Time Insights: Monitoring equipment in real-time allows for timely interventions based on actual conditions rather than set intervals.
- Historical Data Analysis: Reviewing past performance data helps in predicting future maintenance needs, enabling more effective scheduling.
Integrating data into maintenance planning ensures that decisions are grounded in factual evidence rather than assumptions.
Predictive Maintenance Technologies
Predictive maintenance technologies take data-driven approaches a step further by employing advanced algorithms and sensors to forecast when maintenance should occur. This proactive strategy includes:
- Condition Monitoring: Utilizing sensors to track equipment performance, allowing teams to address issues before they escalate.
- Machine Learning Algorithms: These tools analyze vast amounts of data to provide accurate predictions about equipment failures.
By using predictive maintenance, organizations can tailor their schedules more accurately, leading to enhanced reliability, reduced costs, and fewer disruptions. This shift not only optimizes equipment usage but also fosters a culture of continuous improvement within organizations.
Implementing a Custom Maintenance Schedule
Setting Priorities
Implementing a custom maintenance schedule begins with setting clear priorities. Not all equipment carries the same level of importance, and understanding which assets are critical to operations can streamline the maintenance process. Key steps include:
- Identifying Critical Equipment: Focus on machinery that significantly impacts production or incurs high repair costs if it fails.
- Risk Assessment: Evaluate the likelihood and impact of potential breakdowns to prioritize maintenance tasks effectively.
By establishing a hierarchy of priorities, organizations ensure that their resources are allocated efficiently, mitigating risks associated with equipment failure.
Monitoring and Adjusting
Once a custom maintenance schedule is in place, continuous monitoring and adjusting are vital for success. This adaptive approach involves:
- Regular Reviews: Assessing the effectiveness of the maintenance schedule based on performance metrics and operational feedback.
- Flexibility: Being prepared to adjust schedules based on new data, changes in equipment usage, or unexpected situations.
By maintaining a proactive stance on monitoring and adjusting maintenance plans, organizations can respond to changing conditions swiftly. This ensures that the maintenance strategy remains relevant and effective, contributing to long-term operational success.
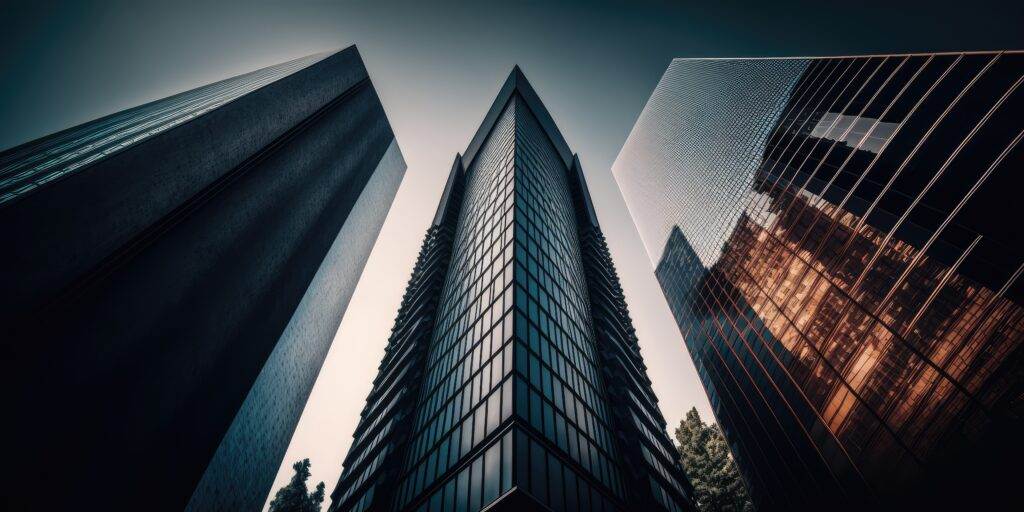
Case Studies: Maintenance Optimization Success Stories
Industry Examples
Exploring case studies showcases how tailored maintenance schedules can lead to remarkable optimization across various industries. For instance:
- Manufacturing: A leading automotive manufacturer implemented a predictive maintenance program, using sensors to monitor equipment health. This proactive approach significantly reduced machine downtime and improved assembly line efficiency.
- Healthcare: A major hospital focused on optimizing its medical equipment maintenance. By prioritizing critical devices, it enhanced patient safety and compliance with health regulations while ensuring minimal disruption to healthcare services.
These examples demonstrate that a structured approach to maintenance can yield benefits tailored to specific industry challenges.
Quantifiable Results
The success stories in these industries reveal quantifiable results that speak volumes about the effectiveness of tailored maintenance strategies. Consider these highlights:
- Reduced Downtime: The automotive manufacturer recorded a 30% decrease in unplanned downtime, translating to significant savings in lost productivity.
- Cost Savings: The hospital achieved a 20% reduction in maintenance costs by focusing on preventative measures instead of reactive fixes.
By analyzing these case studies, organizations can see the powerful impact a strategically implemented maintenance schedule can have, encouraging them to adopt similar practices for improved operational efficiency and financial performance.
Challenges in Maintenance Schedule Optimization
Resource Constraints
One of the most significant challenges in optimizing maintenance schedules is navigating resource constraints. Organizations often face limitations in:
- Personnel: Insufficient staff can hinder the execution of a thorough maintenance program, making it difficult to adhere to scheduled tasks.
- Budget: Tight budgets may restrict the ability to invest in necessary tools, technologies, or training for maintenance teams.
Effectively managing these constraints requires careful planning and prioritization to ensure that essential maintenance tasks are completed without overwhelming the workforce.
Balancing Cost and Effectiveness
Another challenge lies in balancing cost with effectiveness. While it’s tempting to reduce maintenance expenses, this often leads to:
- Increased Risk of Failures: Cutting corners may result in more frequent equipment breakdowns, ultimately costing more in repairs and downtime.
- Quality of Work: Rushed or poorly executed maintenance can lead to short-term savings but may impact long-term reliability.
To strike an effective balance, organizations should focus on value-driven maintenance strategies that align budget constraints with the effectiveness of maintenance practices. By analyzing both short-term and long-term consequences, businesses can develop more robust and forward-thinking maintenance schedules.
Future Trends in Maintenance Optimization
Artificial Intelligence Applications
As we look ahead, one of the most promising trends in maintenance optimization is the integration of artificial intelligence (AI). AI-driven tools can analyze vast amounts of data to enhance decision-making processes. Key applications include:
- Predictive Analytics: AI algorithms forecast potential equipment failures, allowing maintenance teams to act preemptively.
- Automated Scheduling: AI can automate maintenance scheduling, ensuring that resources are utilized most effectively while minimizing downtime.
By harnessing AI, organizations can evolve from reactive maintenance strategies to a more proactive approach, ultimately improving operational efficiency.
IoT Integration
The integration of the Internet of Things (IoT) is another groundbreaking trend shaping the future of maintenance optimization. IoT devices equipped with sensors provide real-time data that can transform maintenance practices:
- Condition Monitoring: Devices continuously collect performance data, notifying teams of any irregularities that require attention.
- Remote Management: Maintenance teams can manage and analyze equipment health remotely, streamlining processes and reducing the need for on-site visits.
As IoT technology becomes more prevalent, organizations can gains deeper insights into their equipment’s condition, allowing for smarter, data-driven maintenance strategies that enhance productivity and extend asset lifespans. By embracing these trends, businesses position themselves to thrive in an increasingly competitive landscape.
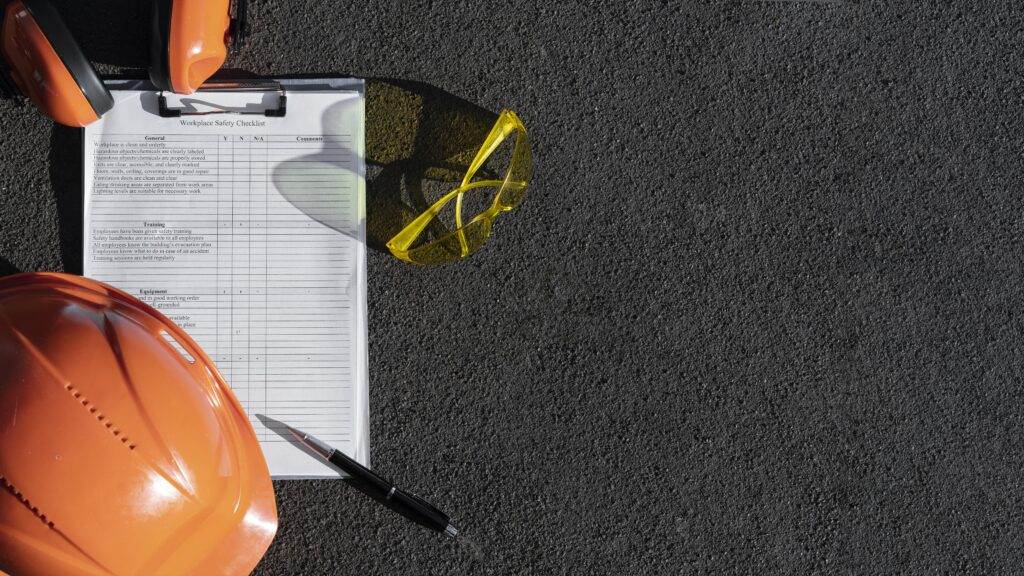
Conclusion
Recap of Key Points
In summary, optimizing maintenance schedules is an essential strategy for enhancing operational efficiency and reducing costs. Throughout our discussion, we explored:
- The Importance of Maintenance Schedules: They are critical for ensuring equipment reliability and performance.
- Tailored Approaches: Leveraging data-driven methods and predictive technologies allows for proactive maintenance strategies.
- Challenges: Balancing resource constraints and financial considerations is key to successful implementation.
These components collectively contribute to a robust framework for maintaining equipment and assets effectively.
Importance of Continuous Improvement
Lastly, the journey of maintenance optimization does not end with implementation. Continuous improvement is vital in adapting to technological advancements and evolving industry standards. Organizations should:
- Regularly Review and Adjust: Based on performance data, maintenance strategies should be updated to reflect changing conditions.
- Invest in Training and Development: Empowering staff with knowledge of the latest technologies keeps maintenance practices relevant.
By fostering a culture of continuous improvement, businesses can not only enhance their maintenance practices but also ensure sustained growth and resilience in an ever-changing landscape.